Growing Together
Nuestro capital humano es uno de los elementos que nos distingue de la competencia y nos aporta un valor añadido en nuestros procesos.
Iniciativas para el desarrollo
Creciendo Juntos
En Gonvarri realizamos proyectos en Formación y Desarrollo, Estilo de Liderazgo, Compensación y Beneficios, Comunicación, Organización del trabajo, Cultura y Clima, Empresa Saludable y Compromiso, entre otras.
Por ejemplo, en Estilo de Liderazgo y Formación se ha desarrollado un programa de desarrollo de alto potencial, llamado Gonvarri Leadership Program y se promueve la promoción interna con la publicación de las vacantes entre nuestros empleados. Para impulsar un estilo de vida saludable, entre otras cosas, se promueven eventos y carreras deportivas, etc.
Esto es una pequeña muestra de las iniciativas desarrolladas. En Gonvarri nos orientamos hacia la mejora continua, evaluando los resultados de estas iniciativas con nuestra Encuesta de Clima.
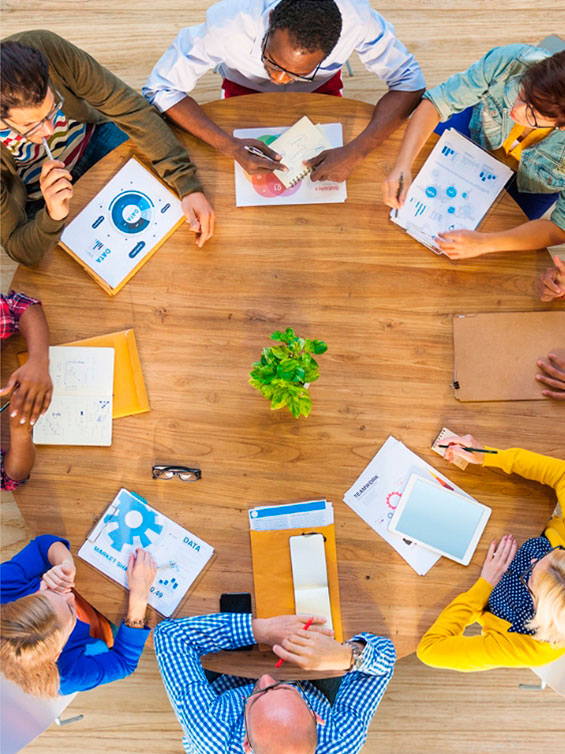
Estilo de Liderazgo
Gonvarri ha creado programas específicos de desarrollo profesional para personas con alto potencial, tales como, Gonvarri Leadership Program, para directivos y mandos intermedios con el objetivo de crear un estilo gerencial propio.
Impulsados por nuestra estrategia de diversificación geográfica, Gonvarri Industries cuenta con plantas operativas en varios países, y como tal, hemos ampliado nuestras capacidades productivas.
Para estas tareas hemos creado paneles de expertos especializados en el arranque de planta y/o puesta en operativo de líneas, los Equipos de Arranque.
Para garantizar la correcta operación de nuestras plantas de manera estandarizada y unificada se crea la Escuela de Supervisores. De esta forma, se promociona a nuestros profesionales.
Formación adaptada a todos los niveles y perfiles
Formación y Desarrollo
Gonvarri Industries apuesta por la formación encaminada a desarrollar el talento como pilar fundamental. Prioriza la formación adaptada a todos los niveles y perfiles formativos de la compañía, de manera global, abarcando todos los centros de trabajo.
Nos centramos en que las personas puedan desarrollar nuevas competencias para estar siempre alineados con el negocio, y que puedan conocer y profundizar en el conocimiento de la compañía para ser más competitivos.
Alguno de nuestros proyectos más destacados es el de Expertos Internos, porque sabemos que transmitir el conocimiento y que no se pierda en una compañía internacional y que crece cada día es fundamental, por ello impulsamos la formación interna a través de un grupo de expertos por áreas, que asumen el rol de formador.
Dentro del desarrollo profesional tenemos planes de polivalencia interdepartamentales, así como planes de rotación.
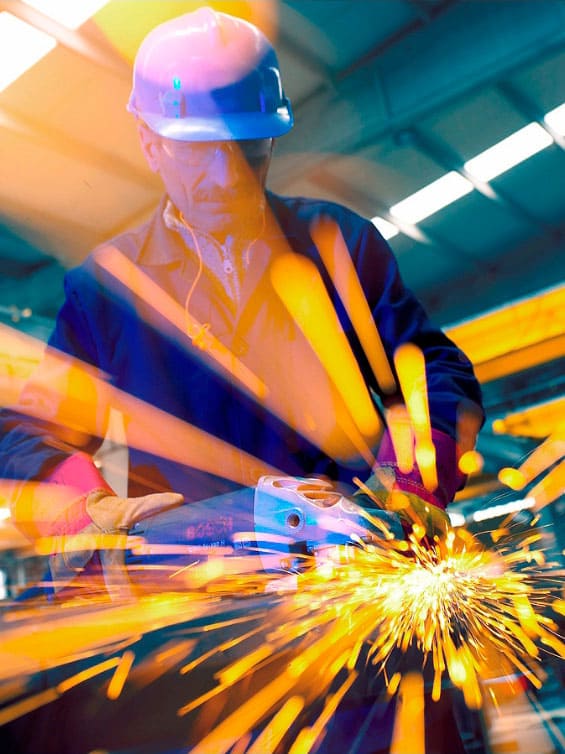
MODELO OPERATIVO TRANSVERSAL
Organización del Trabajo
En una compañía internacional y del volumen de Gonvarri Industries, es fundamental que los objetivos estratégicos estén alineados con los personales.
Para ello, estamos implantando progresivamente la Dirección por Objetivos en toda la compañía, lo que nos permite realizar una adecuada planificación y seguimiento de los objetivos a alcanzar, para conseguir de forma eficiente las metas del negocio.
Cada vez hay más procesos transversales que requieren de la acción combinada de diferentes departamentos y centros de trabajo, por lo que para nosotros es imprescindible una colaboración bien sincronizada y coordinada entre departamentos.
Un ejemplo de ello es nuestro Modelo Operativo Transversal que ha sido capaz de conectar eficientemente la totalidad de todos los departamentos para una gestión eficiente.
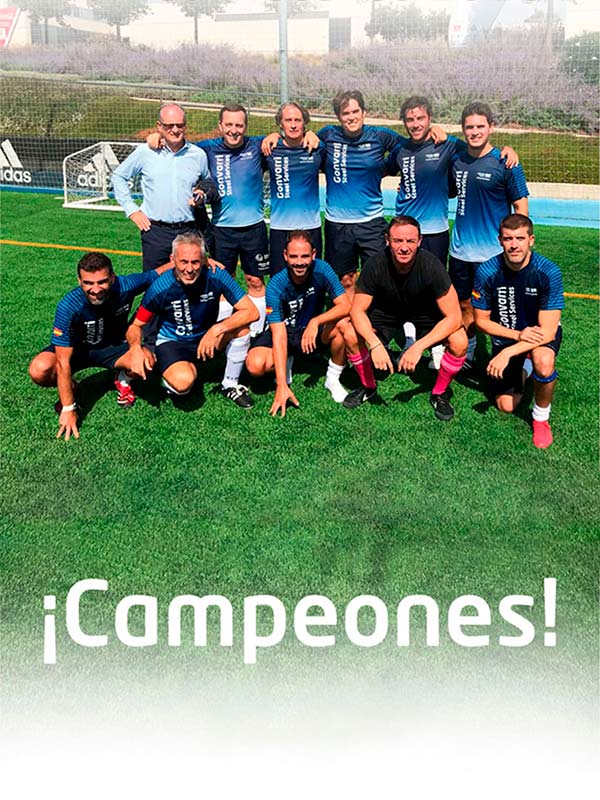
La salud como referencia
Empresa Saludable
En Gonvarri siempre nos ha parecido muy importante promover actividades e iniciativas dirigidas a fomentar la actividad física y los hábitos saludables. Queremos darle un nuevo impulso, dando entidad propia a un modelo de empresa saludable que recoge algunas de las iniciativas que se han llevado a cabo e incorporando otras áreas nuevas y programas enfocados a que Gonvarri viva y sienta los valores de una empresa saludable.
Las personas pasamos una parte considerable de nuestro tiempo en el lugar en el que trabajamos. Nuestra forma de vivir y estilos de vida nos acompañan también al puesto de trabajo de manera que si no fumamos, comemos mejor, hacemos deporte, prevenimos el sedentarismo relacionado con el trabajo o mantenemos una postura adecuada durante nuestra jornada laboral, estaremos incidiendo en nuestra salud y bienestar.
Somos conscientes de que las empresas saludables son más competitivas, las personas que la forman se sienten más satisfechas y que además, generan un impacto positivo en el país en el que están, ayudando a reducir el coste sanitario, entre otros, y nos gustaría ser un ejemplo de todo ello. Queremos que en Gonvarri se adquieran y promuevan hábitos, prácticas y conductas saludables, para ser más competitivos, disfrutando de una vida laboral más completa.
Gestión del Cambio
Nuestra compañía está en permanente cambio adaptándonos a las necesidades y requerimientos cambiantes de nuestros clientes y operando en un mercado global complejo. Por ello desarrollamos diferentes capacidades y competencias en nuestros empleados para liderar cambios y gestionar con habilidad las diferentes transiciones a las que se enfrentan adaptándose sin dificultad a nuevos roles que deben asumir para asegurar y alcanzar los objetivos del negocio.
BIENESTAR PARA LAS PERSONAS
Cultura & Clima
Gonvarri ha puesto en marcha diferentes políticas con el objetivo de promover una cultura responsable en la gestión de personas para que se tengan en cuenta la igualdad de género, como la satisfacción de las personas y una gestión del talento más humana, eficiente y productiva.
En Gonvarri, sensibles a las necesidades familiares actuales, contamos con una serie de medidas relacionadas con la conciliación y flexibilidad laboral en apoyo a las familias de los empleados.
Las medidas contemplan, entre otras, reducciones de jornada, flexibilidad horaria, jornada continuada de verano, flexibilidad en vacaciones, movilidad internacional, retribución flexible, permisos por maternidad y paternidad. Con todas estas medidas contribuimos a construir un clima laboral positivo.
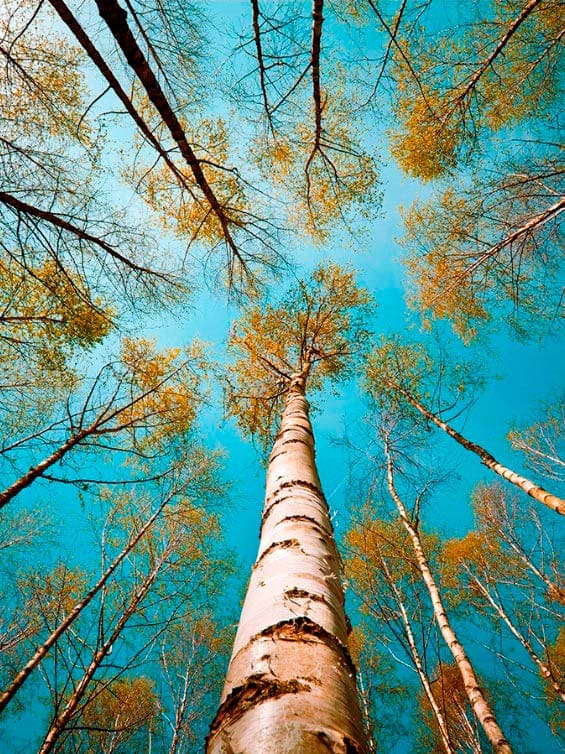
Compromiso
En Gonvarri somos conscientes de la importancia y el valor diferencial que tiene el compromiso y el sentido de pertenencia de los empleados, por ello fomentamos las relaciones de valor entre las personas que forman parte de la compañía, y llevamos a cabo iniciativas en este sentido, que van desde priorizar la promoción interna, el reconocimiento a la trayectoria laboral, a eventos y celebraciones anuales en los que participan las familias de los empleados, siempre bajo nuestros valores fundacionales: Honestidad, Humildad, Tesón y Trabajo.
cOMPROMETIDOS CON LA SEGURIDAD
Traveller's Backpack
En Gonvarri Industries estamos convencidos de que las personas son nuestro activo más importante, y por ello la Seguridad y Salud Laboral viene siendo desde hace tiempo una prioridad en el día a día de nuestro Grupo, tal y como establece nuestra Política corporativa definida al respecto.
Por ello, y con el objetivo de ayudar a anticiparse a otro tipo de riesgos que provienen de los desplazamientos que realiza cada vez más gente y con más frecuencia en nuestro Grupo, hemos creado la plataforma de información “Traveller’s Backpack”.
Por ello y con el fin de mantener perfectamente informados a nuestros colaboradores, y ya no sólo dentro del estricto ámbito laboral físico, hace casi un año se lanzó el proyecto Emotional Driving Challenge, queriendo reforzar nuestro compromiso con la Seguridad y Salud de nuestros Trabajadores en este caso en lo referente a los desplazamientos por carretera (hay que considerar que uno de cada tres accidentes laborales mortales se producen a causa del tráfico).
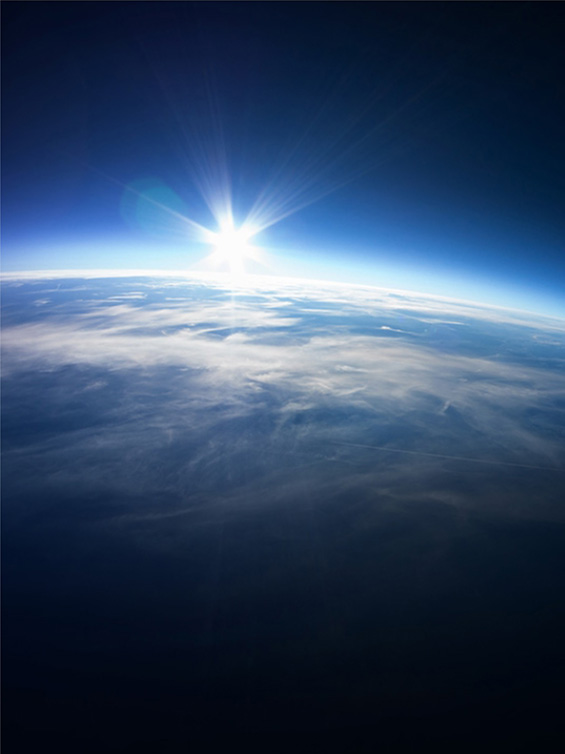
En ella se incluye información relevante de los distintos países a los que viajamos, incorporando para cada uno de los mismos referencia a la documentación acerca de los trámites y visados que se requieren, información actualizada de los riesgos, medidas de seguridad a tener en cuenta en las plantas de destino, puntos y direcciones de interés, medidas acerca de cómo actuar en caso de emergencia, usos y costumbres, consejos médicos e higiénicos, recomendaciones de funcionamiento en cada zona, personas de contacto del Grupo en cada país…
En general, toda la información que hay que conocer previamente, durante, e incluso a la vuelta de estos desplazamientos.